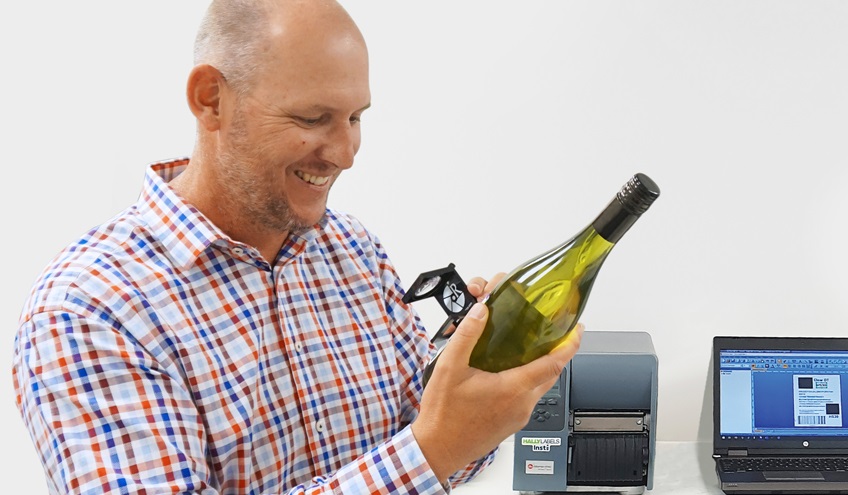
Our custom-built label testing laboratory
The depth of labelling expertise within Hally Labels is world-class. A unique local resource that sets us apart and allows us to deliver technical support to our clients is the Hally Labels Laboratory. Based at our Christchurch factory, our custom-built laboratory is dedicated to testing, analysing and understanding our labels across all industries and challenges.
This invaluable resource allows us to support our clients with an industry-leading research and development service. We rigorously screen new materials and products before launch, conduct comparative and quality control tests, and perform quality investigations. This ensures we specify the right labels for your unique labelling requirement, whether it be an unusual application surface, a difficult application environment, or a challenging supply chain.
Our experienced technologist uses specialist and customised equipment specific to labels to perform a wide range of tests. Many of the tests we perform are accredited and meet international standards such as FINAT and ISO. We also develop specialised and proprietary testing programs to solve the unique labelling challenges of our clients. If you are having label issues, thinking about altering your labelling process, or wanting to seamlessly change a material construction, we can help.
Here we share a snapshot of the custom testing we perform in our laboratory including a glimpse inside the lab – check out the photo gallery at the end.
- Material identification –determines specific face stocks or constructions.
- Adhesion testing – measures the peeling or bond strength of the adhesive and assesses the initial tack.
- Application performance – investigation of a labels ability to release from the liner on application machines.
- A variety of moisture-related tests:
- Water spray test - measures the amount of water that is absorbed into the surface of the label to assess how well the label will stay adhered in cold, wet and condensated environments.
- Cobb test - measures water absorption and the effectiveness of the paper top sheet to repel the water, mainly used in the wine industry.
- Ice Bucket test –a test specific to the wine industry that measures the performance of a labelled bottle immersed in a water and ice bath. This determines the label’s stability and resistance to damage during storage in an ice bucket.
- Moisture resistance test – measures the amount of moisture that is absorbed into a labels top sheet or coating using a mix of isopropyl alcohol solution and water. This is particularly useful when a product is going to be stored in a fridge or cool store situation.
- Thermal performance – measures direct thermal print durability and image quality.
- Environmental stability - tests to suit a variety of factors such as UV stability, compostability, freezer, steam, heat, water, or weather.
- Chemical resistance –measure the labels resistance to oil, plasticiser, acid, and alkaline.
- Conditioning assessment – measure the printed labels performance on product under extreme environmental conditions such as hazardous materials, direct exposure to chemicals, and extreme temperatures.
- Quality control – measures the coating levels, laminate adhesions, dine levels and die strike.
- Slip test – measures how slippery the surface of a coating or ink is to ensure optimal shrink sleeve application.
- Transportation simulation – we even have a machine that simulates what happens to a carton of product when shipped via road, to measure the impact of transport on the label in the supply chain.
- Custom evaluations – testing and evaluation specific to a client’s business to ensure labels are fit for their intended purpose.
Our team of label experts are uniquely qualified to solve your labelling challenges - we’d be delighted to work with you.